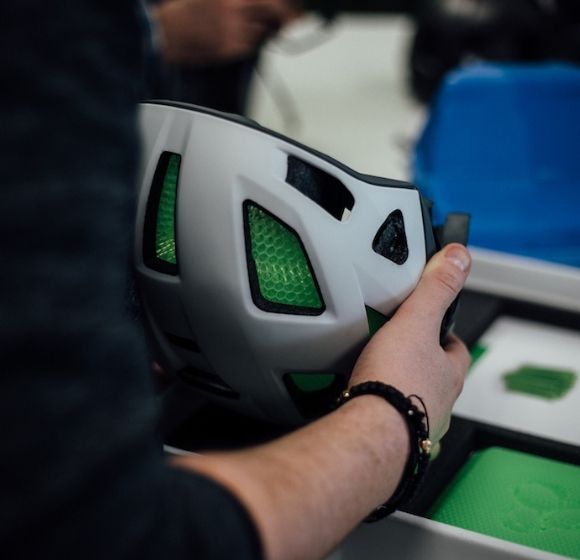
THE MT500 HELMET
Endura's groundbreaking Koroyd collaboration
SOPHISTICATED SIMPLICITY
Simplicity is the grail in any field of endeavour you care to mention.
That a plastic tube (though one admittedly in which every aspect is highly engineered) should dissipate the sudden and potentially catastrophic force of impact so efficiently is proof that less is almost always more.
A core of optimised, welded tubes, that through a period of development and testing have become a technology known as Koroyd, lies at the heart of Endura’s new MT500 Helmet; a product that, even at a glance, clearly embodies the maverick Scots’ philosophy of Renegade Progress. Such dramatic innovation is not arrived at by following the herd.
The advantages of Koroyd’s beguilingly simple impact absorption technology are manifest and infinitely adjustable. The diameter of the tubes, wall thickness, density, angle, even the base polymer, can all be optimised to absorb different types of impact. The driving force that defines which of these variables takes on the greatest significance, however, is the client.
Step forwards Endura. The MT500 Helmet is a full step ahead of the massed ranks of ‘me too’ EPS-lined helmets that have been the cycle industry’s default for 20 years, courtesy of a striking, feature-rich design that complements the lightweight, breathable and incredibly absorbent matrix of thermally welded tubes that lie, figuratively and literally, at the centre of its design.
THE LESS THAN FIVE PER CENT
We live in strange times, in which technology is often in advance of safety, and allowed to be so.
Consider the modern mountain bike - your mountain bike, in all probability. Lighter, faster and more agile than anything you might have dreamed of 20 years ago, today’s trail bike is a machine so advanced that terrain of almost of any severity, no matter how steep, twisted, rocky, or tree-lined can be ridden fast and aggressively.
Now consider your EPS-lined helmet. How different, honestly, is it from the one in which you hit the trails in 1997, when machines like Cannondale’s Super V Raven represented the bleeding edge of mountain bike technology? Why, then, have the safety criteria required to bring a bicycle helmet to market not been updated?
Similar questions have concerned Dr Priya Prasad, a fellow of the American Institute for Medical and Biological Engineering, for more than forty years. He has analysed automotive accident data to develop, with Dr Harold Mertz, a series of “risk curves” - predictors of skull fracture or traumatic brain injury.
The Prasad/Mertz curves have been adopted by the European New Car Assessment Programme to set acceptance criteria for head injuries in a host of crash standards, and are frequently used in conjunction with the Head Injury Criterion (HIC), which measures the likelihood of head injury arising from impact by evaluating not just the maximum amount of energy, but also the total amount of energy over a given time.
Even the numbers for certified technologies are alarming. The maximum HIC value for motorcycle helmets that meet European safety standards is 2,400; or, to put it another way, a value that would place the rider inside the helmet at a 97 per cent risk of severe traumatic brain injury at the test standard’s reference velocity; or, to put it another way again, at a 77 per cent risk of fatality.
Taking the initiative
In a bid to significantly reduce such alarming rates of injury, Koroyd has adopted, voluntarily, the Prasad/Mertz risk curves, and has developed its technology by using the same HIC metric adopted by the automobile industry, with the same goal: to reduce the risk of fatal traumatic brain injury to less than five per cent.
The tests have been encouraging. By placing their core inside cycle and motorcycle helmets, Koroyd have reduced the maximum deceleration of reference impact velocities to under 183g - substantially less than the 250g allowed by European standards and the 300g accepted in America.
The reduction in impact reference velocity delivered a concomitant reduction in HIC value, lowering it to less than 1,666: a figure that correlates to the much sought after ‘less than five per cent’ risk of skull fracture or severe traumatic brain injury.
Further tests involved fitting a Koroyd core inside a high-end, ‘EPS-based’ motorcycle helmet. The core reduced maximum deceleration by 32 per cent and HIC value by 58 per cent, further reducing the risk of skull fracture or fatal brain injury to remarkably low levels.
John Lloyd, Koroyd’s managing director, is leading by example in working with partners like Endura to create helmets that comply – voluntarily - with the lower limits for maximum deceleration used by the automotive industry.
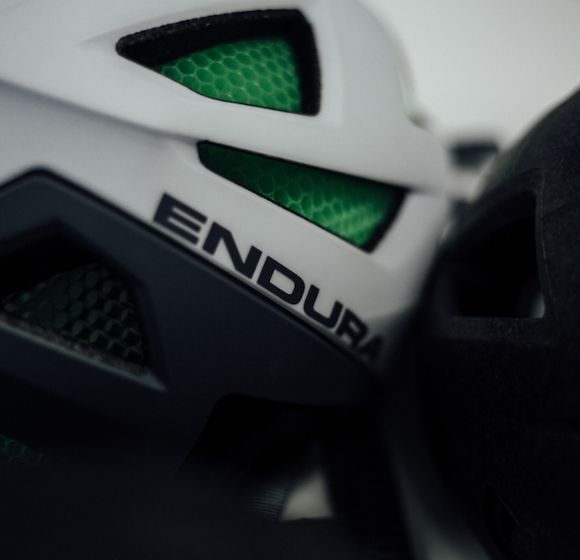
THE KOROYD CONNECTION
At first glance, it is difficult to identify a potentially lifesaving technology in a small plastic tube, but for Lloyd, formerly the head of a product development team at a company making protection products for motorcyclists, spotting such potential is his job, in the most literal sense.
In his previous role, he had grown accustomed to presentations of new technologies, few of which, he recalls, matched the claims of the presenter. The technology that he has since developed into Koroyd was different, however.
Its inventor Peter Sajic had based his idea on research conducted in the aftermath of the Kegworth air disaster of 1989, an accident in which a Boeing 737-400 made an emergency landing on the embankment of the M1 motorway, after failing to reach the runway of East Midlands airport by less than 500 metres. Although the incident happened at comparatively low speed and altitude, the consequences were tragic: 47 passengers were killed, and a further 74 seriously injured.
“This wasn’t a plane that fell out of the sky and had a catastrophic landing. It had a rough landing,” Lloyd observes. “There was a whole body of work done to see if that accident could or should have been survivable, and one of the research projects was to look at energy absorption underneath the seats.
“What they discovered was that the most efficient structure to absorb energy in the bottom of the seats is a tube. We now know that’s because of the way a tube buckles and collapses. For its length, it can absorb an enormous amount of energy.”
The material from which the tube is constructed is critical. Aluminium and composite tubes, materials on which those inspired by the Kegworth air disaster to improve safety had focused their efforts, were found to be too stiff. The welded tubes at the centre of Koroyd’s technology, extruded and then formed from an inner and outer core by a process of thermal welding, make them extremely compressible. Furthermore, they collapse homogeneously; which is to say, at the same rate and in the same manner.
DISSIPATION AND PURE INNOVATION
It is the ability of Koroyd’s tubes to crumple under impact that makes them such effective convertors of the kinetic energy generated by impact. By contrast, imagine the velocity required to crush an aluminium tube of equivalent length and thickness.
Additionally, a Koroyd core - a construction formed by thermally welding thousands of individual tubes together - is itself extremely flexible, and, crucially for Endura’s purpose in creating wearable protection products, can be shaped into curves.
“There’s no black magic, or mystery about how it works,” Lloyd says. “It’s all based on the principles of engineering and physics. The crushing and collapsing of the tubes - there’s a lot of science behind it.”
Pure innovation
What might be described as pure innovation is challenging, almost by definition. The mundane does not disturb preconceptions in the same way as the radical. To the layman, the ability of a technology that closely resembles the humble drinking straw to reduce the impact of serious collisions might not be immediately apparent, but Lloyd insists that keeping an open mind is essential to recognising something groundbreaking.
Far from feeling sceptical, Lloyd was enthused by the potential of the technology presented to him by Sajic. Independent tests validated the inventor’s claims, inspiring Lloyd to commit fully to the technology and buy the patents.
“I was just very excited, because the numbers we’re talking about were a 30 or 40 per cent improvement, which is drastic,” Lloyd says. “With EPS, which has been used for 40 years, it’s very difficult to achieve step change.”
With design and development director Piers Storey, Lloyd has developed a technology that underpins the Koroyd Helmet Safety Initiative, and which lies at the centre of the MT500 helmet.
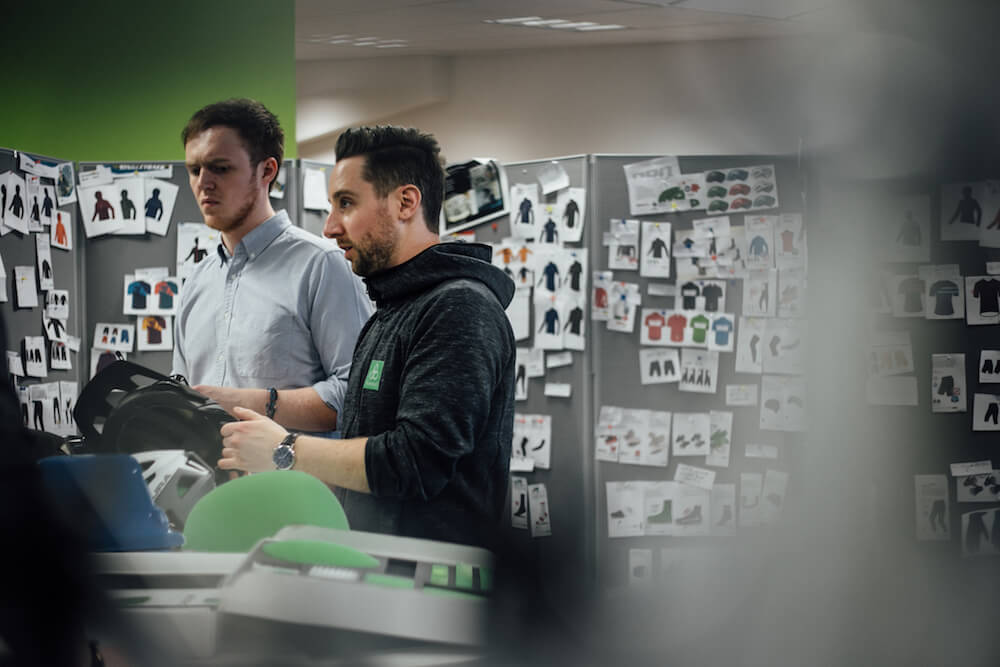
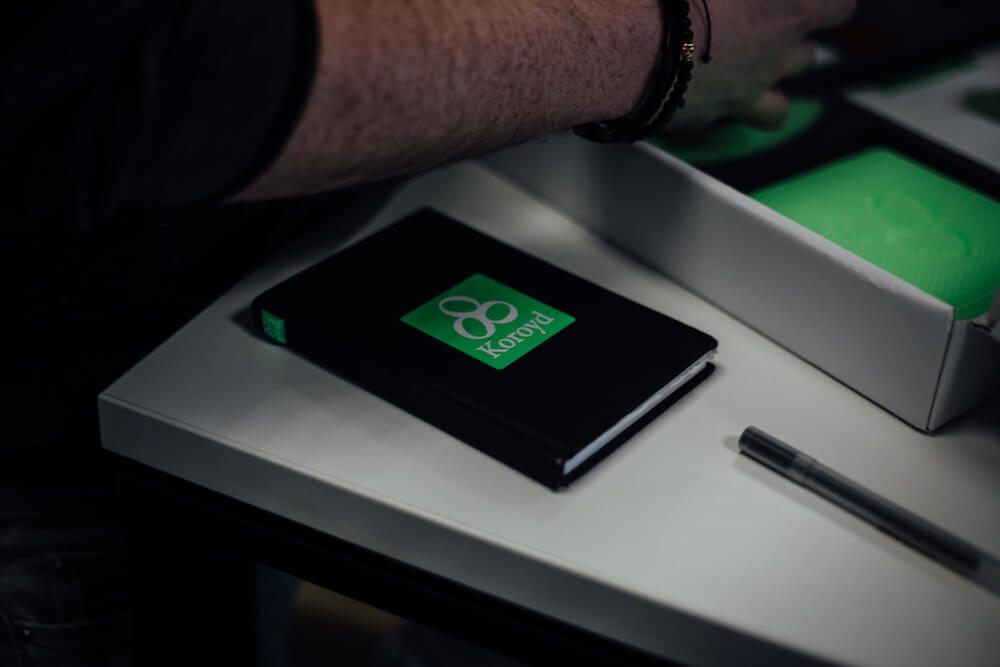
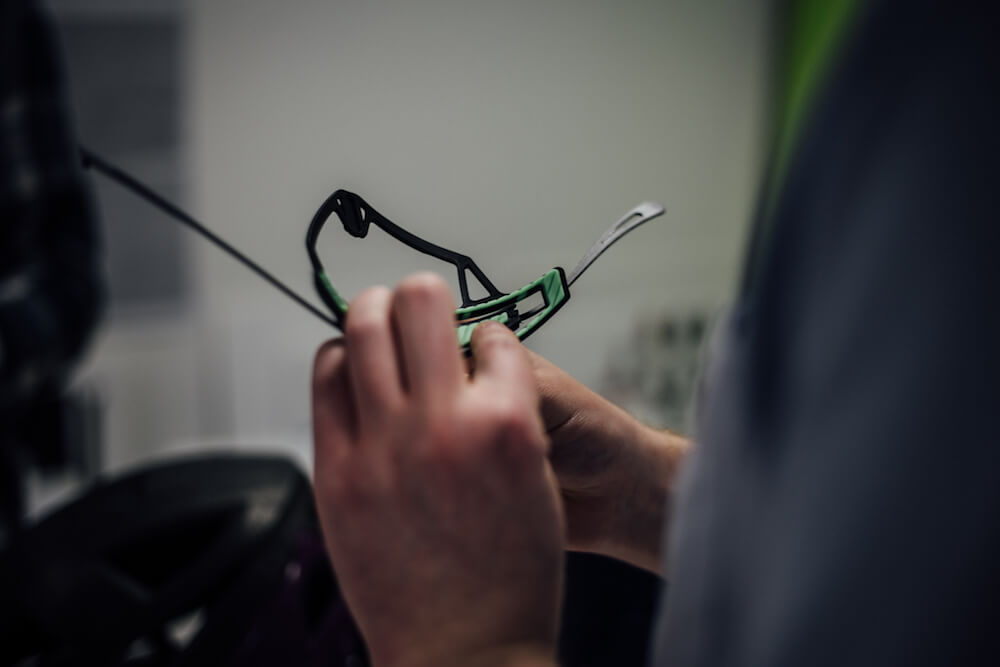
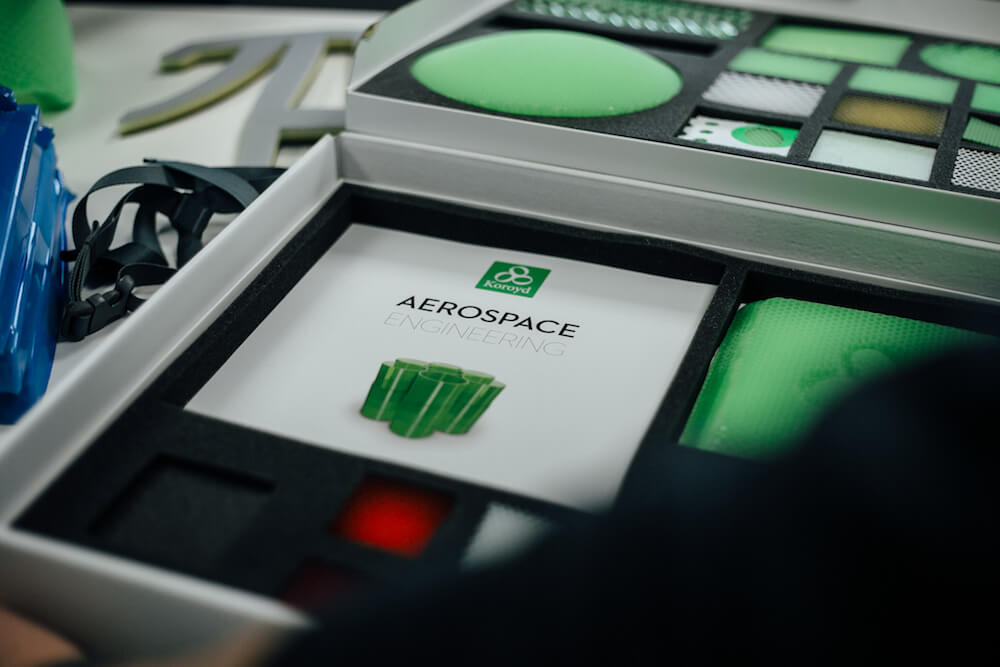
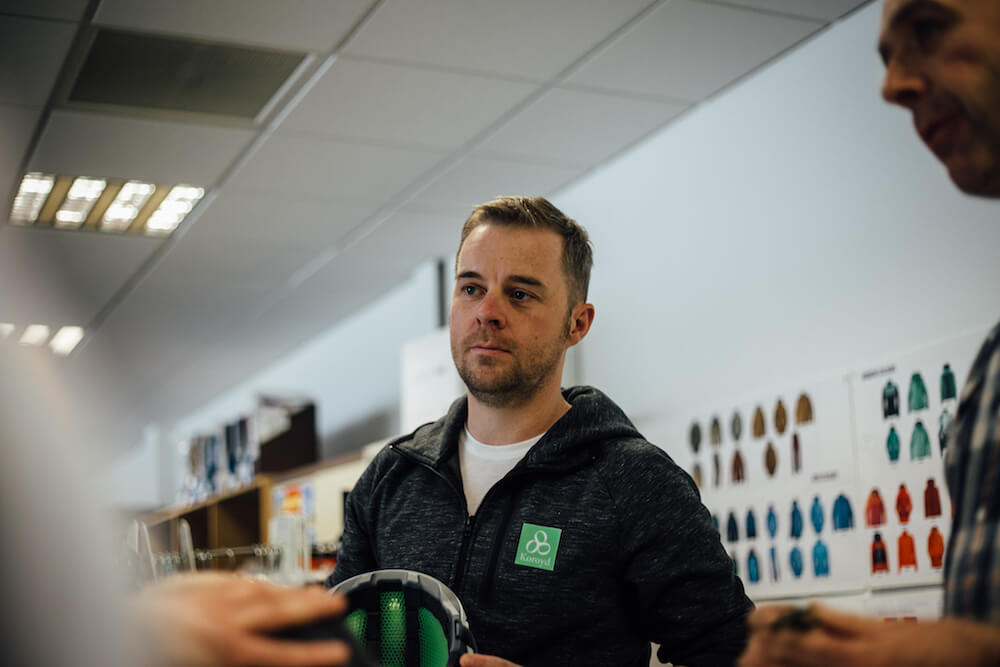
ENTER ENDURA...
Endura is still a comparative newcomer to the helmet market. It’s status in the garment sector, clothing talents as diverse as Movistar Team’s Nairo Quintana and Red Bull athlete Danny MacAskill, is assured. Helmets, however, represented a territory still to conquer.
The renegade Scots’ relationship with Koroyd stretches back to January 2015, when Endura brand manager Ian Young met Lloyd at the ISPO show. At the time, back protectors were the new story in MTB body armour, and the first collaboration between Endura and Koroyd involved the latter’s EOP1 technology, heralded as the thinnest on the market to reach the EN1621-2 standard in both hot and cold conditions.
Endura became the first brand to use the EOP1 in a backpack. Lightweight and exceptionally breathable, it represented a clear advance from the heavier, gel-foam protectors that had dominated the market. More significantly, the EOP1 reached the higher of two levels of certification for back protectors, and, during their conversation at ISPO, Young was soon made aware that exceeding safety norms was Koroyd’s raison d’etre.
“You could see their desire to protect the rider as much as possible,” he recalls. “If you’re making safety equipment, this has to be the key goal, if you’re being honest about it, rather than marketing a product around a story of low weight or breathability. The three aspects need to go hand-in-hand, and, of course, Endura has always placed the greatest importance on function.”
From backpacks to helmets
Reinforcing a backpack is one thing. Incorporating a Koroyd structure into a helmet represents a far greater challenge. Not only does a curved structure present a more significant hurdle to overcome, but the contemporary mountain bike helmet has become an increasingly complex accessory, with advances in technology elsewhere in the cycle industry driving a need for greater functionality.
An example? Action sports cameras weren’t even thought of when the first mountain bike helmets were designed. Powerful lights have become smaller, typically with an integrated battery and beam solution, a technical advance that has made them a wearable technology.
Endura’s approach, as with any product, was to create a design brief, calling on input from internal design and product development teams, and even from the global sales teams, who were able to provide feedback from their own international territories.
Turning a list of features ‘nice to have’ into a working reality requires innovation. Young points to the top-mounted air intake, a unique solution in a crowded market, and one that also doubles as a neat accessory mount for the aforementioned action camera or light.
CHALLENGES AND OPPORTUNITIES
A mere detail? Perhaps, but the air intake/accessory mount offers an interesting example of the challenges presented by incorporating the Koroyd core into the MT500 Helmet: most riders attach a camera or light to their helmet by routing a strap through the open vents of a more commonplace design.
“The integration of Koroyd introduces several issues,” Young explains. “The first is where it is placed; another is how much is used, and how that will help from the perspective of absorbing impact. In the case of the MT500 Helmet, many of those issues were resolved by utilising the knowledge and experience of Piers and John.”
Several parties contributed to turning initial sketches of the MT500 Helmet into the finished reality. Jim McFarlane, Endura’s founder and managing director, was “heavily involved” in the early stages, Young recalls.
Later, Storey refined sketches of the initial concept, following input from Endura’s design and product development teams, notably from Matt Innes. Throughout the process, Endura developed series of CAD drawings to reflect the fast-evolving design and, later, physical prototypes. Given the importance Koroyd place on exceeding existing safety standards, it was natural that they would take the lead on impact testing.
MIND THE GAP
It’s self-evident that the gap between the development of bike technology and helmets must close. Recognising a trend is one thing, however; reacting to it and providing a solution is another.
Endura’s union with Koroyd to create the MT500 Helmet is a bold step towards new levels of rider safety. EPS-lined helmets continue to save lives, but where a measurably better technology exists, it makes every sense to use it.
Even if Koroyd’s impact absorption technology is arguably the MT500 Helmet’s most striking feature, similar innovation lies in the multitude of features that make this a helmet equal in function to the significant step taken towards greater safety.
Lightweight, breathable, supremely safe, and with features including an adjustable visor, eyewear dock, goggle strap clip, and a micro-adjustment system that the rider can use with one hand, without the need even to take off a glove, the MT500 Helmet surely is a design at the very forefront of bicycle helmet technology. Taking risks has never been safer.
© 2021 ENDURA